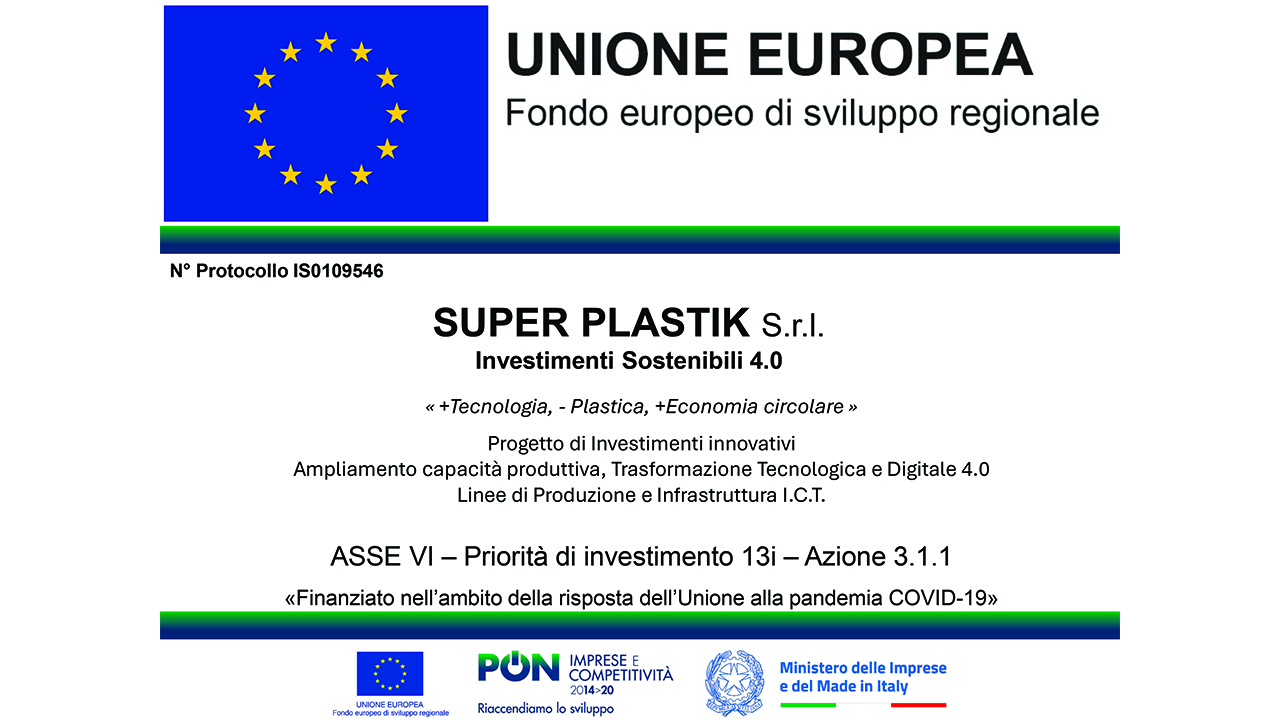
13 Nov PIÙ TECNOLOGIA, MENO PLASTICA, PIÙ ECONOMIA CIRCOLARE
La sostituzione dell’impianto di estrusione comporterà una riduzione dei consumi energetici. I consumi energetici passeranno dagli attuali 0,504KWh/kg prodotto a 0,42 KWh/kg (-17%) su un impianto che oggi consuma circa il 40% dell’energia elettrica utilizzata dall’azienda.
Il consumo globale di energia elettrica aziendale verrà ridotto di conseguenza del 6,68%.
Normalmente per la sostituzione dei filtri della massa fusa è necessario fermare l’impianto con conseguenti ritardi di produzione ma soprattutto con produzione di scarti per le fasi di avviamento che a volte rendono l’uso di materiali riciclati antieconomici (gli scarti prodotti per la sostituzione dei filtri potrebbero essere maggiore del prodotto riciclato utilizzato sull’impianto)
L’impianto è equipaggiato con un sistema di filtrazione della massa fusa di tipo continuo non stop che consente la sostituzione dei filtri senza fermare l’impianto e senza produrre scarti. Tale caratteristica rende l’impianto particolarmente adatto all’utilizzo di materiali riciclati.
Le nuove teste di estrusione, i moderni sistemi di regolazione dello spessore gravimetrico e con anello con controllo a zona del flusso d’aria garantiscono delle tolleranze di spessore molto più basse sia per quel che riguarda il peso/metro quadro che per le differenze puntuali misurabili sulle film prodotto. Di conseguenza sarà possibile abbassare gli spessori nominale dei film con conseguente riduzione dei consumi di plastica per la produzione di imballaggi.
La nuova saldatrice ha dei sistemi di controllo delle saldature che consentirà all’azienda di produrre buste con materiali più ecosostenibili composti da film multistrato di resine omogenee o monoresina.
Attualmente sugli impianti non è possibile lavorare materiali a causa della mancanza di precisione dei sistemi di saldatura relativamente all’accuracy delle temperature nonché dei tempi di e pressioni delle barre saldanti.
Gli impianto già predisposti per industria 4.0, con una predisposizione hardware e software tale da consentire analisi e teleassistenza da parte dei fornitore non solo per la gestione dei guasti ma anche per ottimizzare i parametri di processo, l’interscambio dei dati di produzione con il sistema gestionale riduce il rischio di errore umano sia nel setup delle fasi di produzione che nel tracciamento dei prodotti finiti nonché delle caratteristiche quantitative e qualitative dei prodotti e delle materi prime utilizzate.